Procter Delivers
Cutting-Edge Enclosure
Designing for Innovation and Global Usability
WAAM3D, a pioneer in wire arc additive manufacturing, required a bespoke enclosure for their RoboWAAM™ system. Their design concept involved several unique requirements:
- Lightweight panels (<15kg) for manual handling
- Complex curves without costly tooling
- A first-of-its-kind single rotary roller door
- Ergonomic operator station with dual monitor setup and adjustable height
- Efficient packaging for global shipment
- A right-first-time approach for a Japanese customer
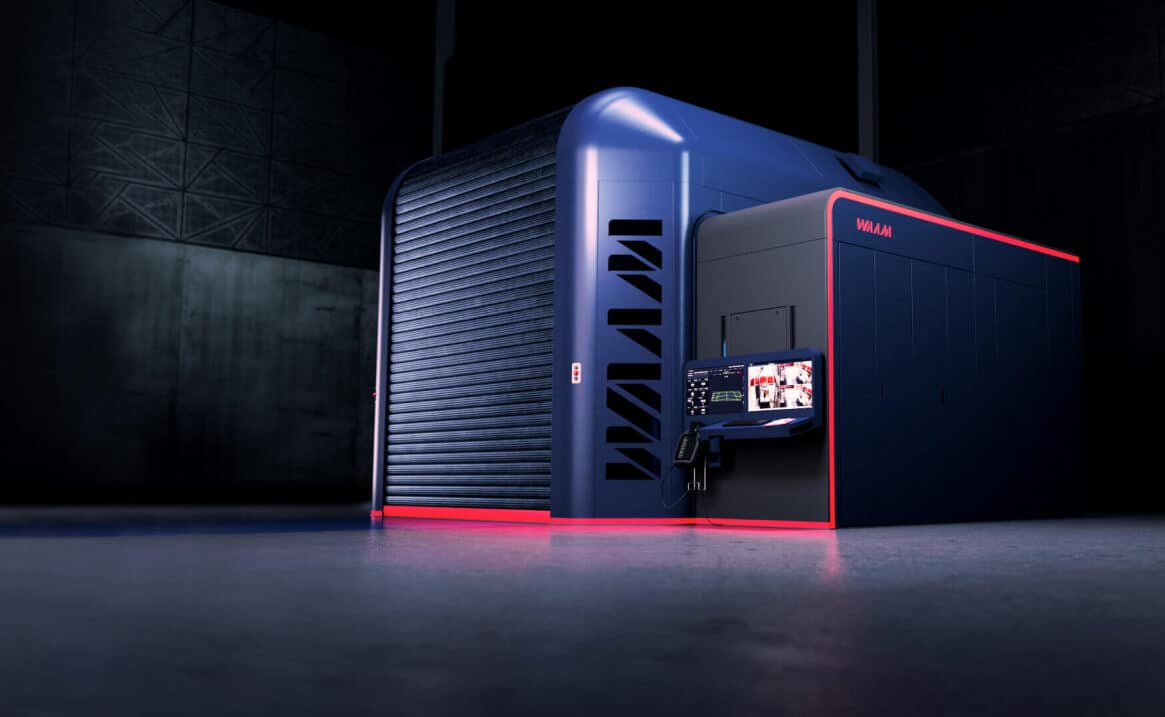
Innovative Engineering Meets Practicality
Procter translated WAAM3D’s concept into a manufacturable solution that balanced innovation, ergonomics, and efficiency.
- Roller Door: A tensioned, electronically controlled design built from off-the-shelf components for global support. A wireless safety edge enhanced operator protection.
- Enclosure Structure: 50x50mm steel box-section frame supporting a 500kg roller door, clad with 2mm steel and aesthetic fibreglass panels for a modern finish.
- Operator Station: Integrated height-adjustable desk, dual-monitor setup, and ergonomic design.
- Packaging & Assembly: All components were efficiently packed into 7 crates, organised for step-by-step assembly and worldwide shipping.
Right-First-Time Success for an Industry Pioneer
Procter Machine Safety delivered a fully compliant, robust enclosure tailored to WAAM3D’s vision. The solution was praised for its innovative design, structural integrity, and user-focused features, helping to bring WAAM3D’s advanced manufacturing system to life for a global audience.