By Jeremy Procter, Convenor of the European Standards Committee responsible for Machine Guards, and Managing Director of Procter Machine Guarding
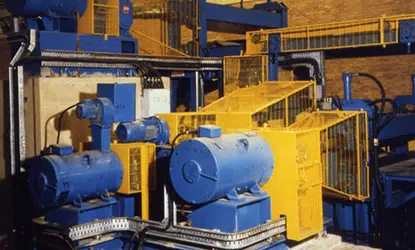
Far-reaching implications of BS EN 294: 1992
One of the most important standards relating to machinery guarding is BS EN 294: 1992, ‘Safety of machinery – Safety distances to prevent danger zones being reached by the upper limbs’, yet many machine builders are thought to be using their ‘best skill and judgement’ rather than working to the standard. This is no excuse, because of compliance with the Machinery Directive – and, subsequently, CE marking – requires adherence with all relevant standards, and BS EN 294 is certainly relevant to most, if not all machinery.
While we normally consider machinery to be something encountered in an industrial environment, readers should be aware that BS EN 294 is intended for designers of machinery that will be used for both occupational and private purposes. And the standard also includes data relating to children aged 3 and above, though such youngsters should not be operating industrial machinery! Furthermore, care should be exercised when applying the standard to machinery destined for export outside Europe because, strictly speaking, the standard only takes account of anthropomorphic data for ‘ethnic groups likely to be found in European countries.’
Risk assessment
As with all matters relating to machinery safety, the first thing to do is a risk assessment. Depending on whether the risks are assessed to be low (such as from friction or abrasion) or high (such as entanglement), there are two tables in the standard that give figures for the height of the protective structure, the height of the danger zone and the horizontal distance to the danger zone. It is important to note that interpolation between the values is not permitted. Nonetheless, the risk assessment should take account of other factors, such as whether the person is likely to stand on a chair, ladder or anything else in order to reach the danger zone, or if the person might be holding something to extend his or her reach. If the barrier alone is felt to be insufficient, additional protective measures must be used. Similarly, it must be remembered that complying with this standard may not provide protection from other hazards such as radiation or ejected parts.
Designers can use the tabulated values in the standard in one of two ways for a given height of a hazard. If a guard of known height is to be used, the required distance from the hazard can be found; or if the distance from the hazard is restricted for any reason, the required guard height can be found.
As well as covering persons reaching over the top of barriers, the standard also carries information relating to fingertips, fingers, hands and arms reaching through apertures of various shapes – including irregular shapes. In addition, there are useful examples of how additional fixed barriers can be used to prevent hazards being reached if, for instance, a person has placed their arm through an opening.
Angel Modular Guarding system
For perimeter guarding applications, Procter Machine Guarding offers bespoke guards or the Angel modular machine guarding system. Already the Angel system has been deployed within factories such as Honda’s Swindon works, but another project was recently completed for the Warwick Manufacturing Group (WMG), the independent centre of excellence within the engineering department at Warwick University.
Angel was selected for a new installation around an automated self-pierce rivet system at WMG. Because of the frequently changing nature of research laboratories, the modular guarding is perfect in that it can be reused, reconfigured or extended quickly, easily and cost-effectively.
Most of the Angel guarding at WMG consists of rigidly mounted posts with infill panels of which the lower half is sheet steel and the upper half is steel mesh. This provides adequate protection but allows excellent visibility of the self-pierce riveter and other mechanical fastening systems that are the subject of current research projects. Access to the approximately seven-metre-square cell is provided via an interlocked door.
The modular guarding required only minimal specification/design input and then, when the system was installed towards the end of 2002, the whole process took no more than a couple of hours. Not only does the finished guard fulfil its safety function, but it also looks very attractive with a striking yellow, black and charcoal grey colour scheme. This is important for WMG because this is also the home of BARA (the British Automation and Robotics Association), which often hosts high-profile visits.
Dr Ken Young, Principal Research Fellow at WMG, is extremely complimentary about the Angel system, saying: “It is ideal for our situation where we regularly need to rearrange the guarding. Shortly we will be extending the self-pierce rivet cell so we will be ordering additional posts and panels. Fitting these will be very quick, and the fact that we can reuse all the existing hardware is crucial to keeping our costs down. I would definitely use Angel again should we need to install more guarding in the future.”
As well as the posts and panels mentioned above, the Angel system also includes clear polycarbonate panels, all-mesh panels, all-steel panels with or without polycarbonate windows, sliding gates, cantilevered gates, and rise-and-fall gates.
Other options include a variety of access controls, integral cable trunking and adjustable base plates. A comprehensive Design Guide is available free of charge from Procter Machine Guarding by telephoning or E-mail Procter Machine Safety.
For more information about BS EN 294 or guarding standards in general, please contact Procter Machine Safety.