The ROI on risk reduction in machine safety – the true cost of money well spent
Procter Machine safety is the UK’s leading machine safety specialists. We have created this overview to present a solid business case for investing in your business’ health & safety risk reduction – with an informative viewpoint of the return on investment (ROI) costs of buying a protective machine guard compared to the serious implications and financial costs of not having a preventative safety measure in place.
Recent Health & Safety Executive (HSE) statistics forecasted that every year over a million UK employees are injured, or made ill by their place of work. This can have catastrophic financial and human costs to the employer and employee, as well as serious implications to society as a whole.
Machine guarding – protecting your business from hazards.
The return of investment (ROI) for an employer in their workplace is second to none. Money spent now results in massive financial and human savings in the future. The goal is to provide today’s business owners and decision makers with an opportunity to gain a competitive advantage via a proven source – investment in your business’s risk reduction systems.
The risk is ever present in the workplace, and those organisations that actively work to identify and reduce it, outperform businesses that are only solely focused on compliance or common injuries. Health and safety executives (HSE) studies have shown a business that is committed to increasing prevention and focussed on risk reduction are the ones who are successful in reducing overall company expenses. Further demonstrating why risk reduction through machine safety is the road to achieving financial & safety excellence.
In, this example a packaging manufacturer contacted us – Procter Machine Safety and asked us to design, manufacture and install a bespoke guarding solution– that would prevent access to a small conveyor nip point, plus provide work to install remote lubrication points that could be accessed from outside the new guarding. Our machine guard solution and service only cost the manufacturing company £1,000.
Financial costs of workplace accidence?
An employer who doesn’t adhere to using safe systems of work, are at risk to being exposed to tens of thousands of pounds of financial costs – Costs that include workplace disruptions, loss of productivity, employee replacement, training, rehabilitation costs, as well as increased insurance premiums and legal costs.
Table 1 – Highlights the costs associated with workplace accidence, and according to the latest HSE cost model- in 2016 the average UK employer paid an estimated £99,700 for fatalities, £6,500 for injuries with more than 7 days absence from work, and £12,300 for work-related ill health with more than 7 days absence from work.
Table 1: Costs to employers per case – average appraisal value estimates
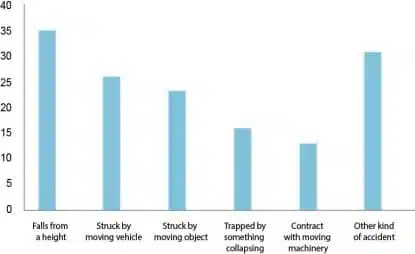
Table 2: Number of fatal injuries to workers by accident kind – 2017/18 (Source HSE)
Table 2 – shows around three-quarters of fatal injuries were a result of just five different accident kinds. According to the 2017/18 HSE results – 35 fatal injuries happened to workers who fell from a height, being struck by a moving vehicle accounted for 26 fatal injuries, 23 where caused by being struck by a moving object, 16 workers where trapped by something, and 13 fatal injuries to workers were due to contact with moving machinery,
In this example a timber manufacturing company was prosecuted after a worker received horrific fatal injuries, resulting in a severing of his left arm when using a crosscut saw. The machine guard had not been properly checked and maintained to HSE standards, so was not fit for purpose. The resulting fatal accident cost the company over £200,000 in financial costs alone.
Badly designed safeguards may also be inconvenient to use or encourage users to override its use, which could cause your employees to risk injury and break the law. If your employees are doing this, find out why and take appropriate action to deal with the reasons and causes.
Machine safety products & Services
Common safety practices employed in the reduction of risk to workers include machine safeguarding. Procter Machine Safety, are experts in workplace machinery safety. Our guards are in compliance with all relevant standards including BS EN ISO 14120 and BS EN ISO 13857. And where appropriate, the guards also comply with standards specific to the type of machinery being safeguarded.
Procter Machine Safety – know what potential injuries moving machines can cause and how to prevent such accidence happening. From workers getting struck and injured by moving parts, sharp edges causing cut and severing injuries, people can be crushed or sustain electrical shocks and burns. These health and safety risks can be easily managed via proper health & safety assessments and training. Procter Machine Safety offer – puwer assessment (Provision and Use of Work Equipment Regulations 1998), as well as design service and installation of new and replacement machine safeguarding systems – machine guards, machine enclosures, access platforms, interlocks and light guards plus many more safety reducing products that adhere to HSE standards, and ISO 9001 Quality Management System.
The overview of information here demonstrates a snapshot of both the potential costs of fatalities, injury and illness, as well as some of the potential benefits of deploying a structured safety program with up-to-date machine guarding, and on-going PUWER maintenance assessments. As with most good investments, the benefits in the long-term—and many times even in the short-term—can outweigh the initial costs. Plus from a less financial and more human perspective, investing in the health and safety of your greatest assets – your employees– is perhaps the strongest case any business decision maker can make.
Procter Machine Safety Background & Summary
Procter Bros have a proud 275-year heritage; we operate from four separate divisions- Procter Contacts, Procter Safety, Procter Cast Stone, and Procter Supplies.
Procter Machine Safety is the UK’s leading specialist manufacturers, suppliers and installers of machine safety products and services. For more details contact us today!
>> Next: New Technical Specification for trapped key interlocks
>> Procter Machine Safety News